
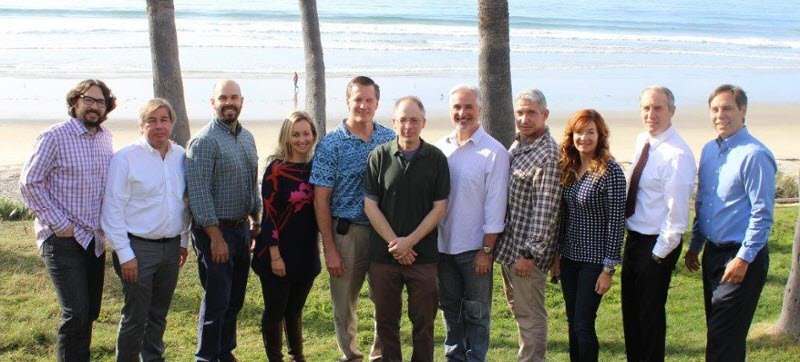
They also connected with Barrack thanks to Kuester. They made the work part of their doctoral research and launched their startup at the same time. “It’s truly inspiring to work with enthusiastic and innovative students in the classroom and the lab and see their ideas and careers take flight,” Kuester said.ĭe Vivo and Pelz both took engineering Frontiers, a graduate-level class taught by Kuester, and later served as teaching assistants and mentors in the class. LIMBER has partnered with the Rotary Club to provide prostheses for local amputees. LIMBER cofounder Luca De Vivo, a postdoctoral student in the Department of Structural Engineering (left), talks to two members of the Calafia Rotary Club in Ensenada, Mexico. Preliminary, proof-of-concept studies with lower-limb amputees have shown the potential of this approach. Dubbed the Limber Integrative Imaging Modeling for Bold Exoskeleton Research Project, or LIMBER, the project’s goal was to bring together imagining, modeling, simulation testing and 3D-printing to create low-cost, one-piece prostheses that could be tailored to match. The project began in 2016 in the research group of Falko Kuester, a professor in the Department of Structural Engineering. They connected with mentors through IGE, including medical device executive Michael Collins. The company will soon start raising a seed round of funding. LIMBER is also part of UC San Diego’s basement startup accelerator. LIMBER has deep roots at UC San Diego: It is currently part of the Medical Technology Accelerator at the Institute for Global Entrepreneurship (IGE) at the UC San Diego Jacobs School of Engineering. They are also conducting testing to make sure prosthetics are safe. LIMBER has conducted several tests to see what kind of loads 3D materials could bear and design their prosthetics accordingly, Barrack said. Materials for prosthetics have improved dramatically over the past 35 years, from wood all the way to space-age materials and materials that can be 3D-printed, said Barrack, who is a certified prosthetist and orthotist. They are also made from water-proof materials, unlike traditional prosthetics made of carbon fiber and metal. The LIMBER devices are comfortable, she said.
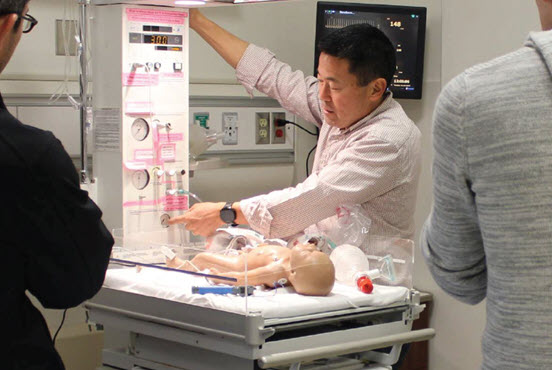
“It’s going to be wonderful to have prosthetics that are affordable for everyone,” she added. LIMBER’s methods will also make prostheses much more affordable – costs currently run upwards of $ 20,000, Zambrano said. “LIMBER can print out a leg in a day, and right away, you have a leg to walk on. “Mobility is a necessity,” Zambrano said. The company will revolutionize access to prostheses for amputees, said Diana Zambrano, a San Diego resident who is an amputee herself and has helped test the devices.Īn amputee tests a LIMBER prosthesis at a clinic in Ensenada, Mexico. The company plans to sell its personalized prostheses in developed countries while providing its services to developing countries at discounted prices or for free. Pelz, De Vivo and Barrack have formed a startup, LIMBER Prosthetics & Orthotics, Inc., to commercialize the technology. Using this combination of personalized scans as well as digital designs and 3D printing can greatly reduce the cost of a prosthesis by anywhere from 50% to 90% and deliver prosthetics much faster to those who need them. Patients have to undergo frequent visits to doctor’s offices and have access to specialists. This is because prosthetic limbs are expensive and time-consuming to manufacture. The World Health Organization estimates that there are 40 million amputees in developing countries, 95% of whom make do without a prosthetic limb.
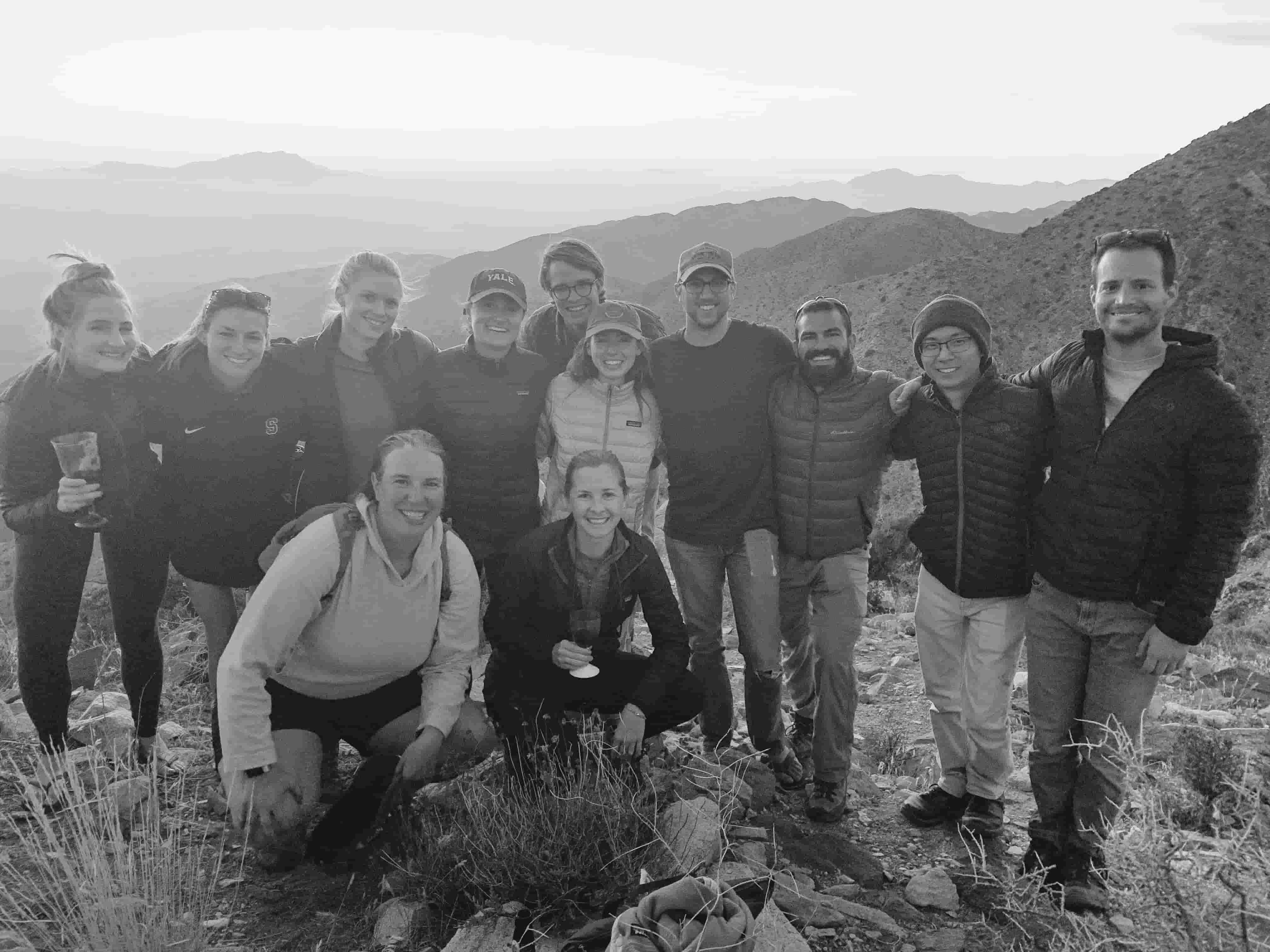
ISHARE UCSD EDU HOW TO
Information on how to make a donation is available on the project’s website. This project is supported by the Rotary Foundation and is looking for other funding sources as well. Photo by Erik Jepsen / University Communications.Īfter the prosthesis is 3D-printed, the team returns to Mexico, where they fine-tune the fit. LIMBER designs and 3D-prints made of custom prosthesis from cutting-edge materials.
